Smart manufacturing is a production strategy that leverages advanced technologies such as the Internet of Things (IoT), artificial intelligence (AI), automation, and big data analytics to optimize manufacturing processes. By incorporating these technologies into their operations, manufacturers seek to improve production rates and product quality while simultaneously reducing costs. Embracing smart manufacturing also helps companies increase their flexibility. With the visibility and data provided by these methods, they can gain better insight into their unique challenges and opportunities for growth.
What Does Smart Manufacturing Have to Do with Equipment Value?
If smart manufacturing is concerned with using modern technology to optimize manufacturing processes, then what does that have to do with increasing equipment value?
The obvious statement that needs to be made here is that the use and maintenance of manufacturing equipment is, in and of itself, a vital element of the production process. Manufacturing equipment is used within the production of goods, ergo, it is directly related to the overall manufacturing process and impacted by smart manufacturing. Automation and artificial intelligence have particular influence on manufacturing equipment, allowing for certain machines to operate or even make simple decisions of their own accord.
But we’re concerned with how smart manufacturing increases equipment’s value, which is a far more specific topic of discussion. Certainly, the benefits of smart manufacturing to this particular aspect are not as readily apparent. But that doesn’t mean they’re unimportant. Increasing your manufacturing equipment’s value means less replacements, less downtime, and a far more effective process overall.
Let's look at how smart manufacturing technology enables these benefits.
Increase Your ROI by Investing in AirFinder OnSite
- Low Cost. AirFinder OnSite XLE is a fraction of the cost of competitors' pricing.
- Long Battery Life. XLE lasts up to 7 years with hundreds of location updates daily.
- Increased Efficiency. Spend less time looking for assets, and more time being productive.
Predictive Maintenance
Predictive maintenance refers to a process of predicting when vital manufacturing equipment will require maintenance, as well as the timely detection of recurring operational errors that might indicate a larger problem. The goal of predictive maintenance is to address equipment failures before they occur or failing that, to catch them before they worsen or have too great an impact on regular operations.
The strategy of predictive maintenance is one of the biggest benefits that smart manufacturing has to offer. Prior to the establishment of predictive technologies, predictive maintenance was based entirely on maintaining regular check-up schedules and intimate knowledge of the equipment being used. The former might be more aptly described as preventive maintenance; the latter becomes a rather reactionary response.
Predictive maintenance has a rather self-evident ability to increase the value of manufacturing equipment. Its whole purpose is, after all, to prolong the lifespan of the equipment (sometimes called RUL, or “remaining useful life”) and to reduce the need for replacements. Smart manufacturing has provided manufacturers with the tools to effectively pursue this strategy so that they can continue to use their existing equipment for years to come.
Utilization Monitoring
Utilization monitoring involves tracking the usage of resources – in this case, manufacturing equipment. The data collected from utilization monitoring is analyzed to identify underutilized resources and optimize their usage. By collecting and analyzing this data, companies are provided with insights into resource utilization patterns, such as peak usage times, underutilized periods, and general rates of process completion. This information is then used to develop strategies to optimize resource usage, reduce downtime, and maximize production.
Smart manufacturing enables better utilization monitoring through automation and IoT. There is nothing about utilization that cannot, in theory, be recorded manually. However, maintaining these manual records is tedious and tends to take up production time in and of itself. By implementing IoT solutions that record and store usage data of their own accord, the true value of utilization monitoring is realized.
In terms of increasing the value of equipment, this improved utilization monitoring means that you can make sure the equipment that you’re spending money to purchase and maintain is actually being used. After all, manufacturing equipment has very little value to a company if it is simply gathering dust and not actually being used for production. Equipment tracking systems can help prevent this eventuality.
Data Analytics
By collecting and analyzing data, companies can identify opportunities for improvement and implement changes that can lead to significant cost savings and increased productivity. The impact of this is seen in both the predictive maintenance and utilization monitoring examples, as they both utilize some form of data analytics. However, the value does not stop there. Data analytics can also be used to inform equipment best practices, energy consumption, and more. And once again, smart manufacturing enables improved data analytics by allowing operators to examine aspects of their equipment use that might have been difficult to analyze regularly when conducting manual inspections.
Data analytics can be a powerful tool for increasing the value of equipment. By using data analytics, you can not only keep track of usage, but also establish best practices for your equipment in hopes of extending its lifespan.
Real-Time Monitoring
Real-time monitoring involves the collection and analysis of condition and location data in order to inform a business’s operations. Real-time monitoring of manufacturing equipment can include any number of data points about that equipment, including location, usage, lifespan, user, and more
All of the aforementioned methods of increasing your equipment’s value are either contingent on or enabled by real-time monitoring. Predictive maintenance requires visibility of equipment status; utilization monitoring requires visibility of both usage and downtime. With this in mind, it is easy to see how real-time monitoring can be improved with smart manufacturing for even greater returns on efforts to increase your equipment’s value. After all, many of the benefits are the same. Real-time monitoring can also help you increase your equipment’s value by keeping you apprised of where it’s located; after all, you can’t use what you can’t find, and it costs money to replace what’s gone. Heavy equipment tracking is particularly important in this regard, as construction equipment and similar machines are particularly prone to theft and misplacement.
Increasing Your Equipment’s Value with Link Labs
Embrace the smart manufacturing technology that enables you to increase your equipment’s value with asset tracking solutions from Link Labs. With our AirFinder Onsite solution, you can take advantage of all the strategies that build off of real-time monitoring that we discussed in this article, plus many more!
Keep track of when and how often your equipment is being used so you can make informed decisions about preventative maintenance, overall utilization, replacements, and more. With effective equipment asset management and the location and condition data that it helps you collect, you can make more informed decisions that can help your business grow and succeed in its mission. If you want to learn more about how this solution can work for you, book a demo today.
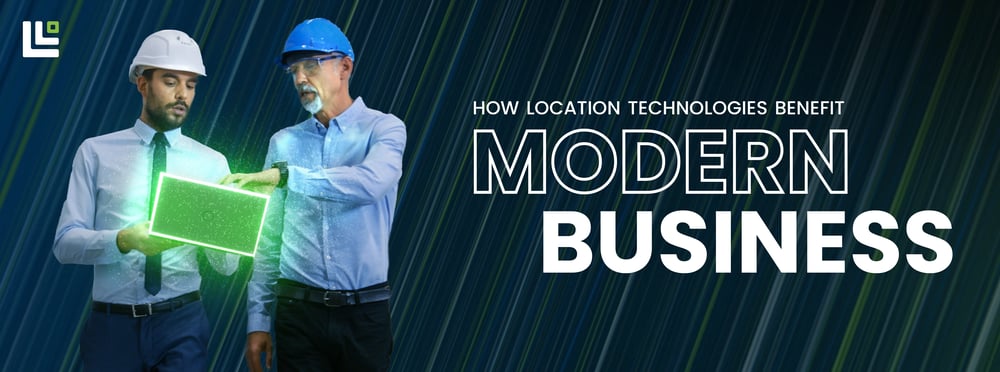