The aerospace industry revolves around exploring the final frontier of space. Research, development, and engineering are all facets of the aerospace industry. Advancements in technology are necessary to ensure the best possible testing and assembling during the manufacturing process. A Real-Time Location System (RTLS) improves manufacturing efficiency for the aerospace industry.
Aerospace Manufacturing
Aerospace manufacturing involves making parts for planes, spacecraft, and rocket or missile systems. These parts require immense precision. Aerospace manufacturing consists of complex processes requiring the highest efficiency possible. A critical facet of the manufacturing process is ensuring that the correct parts are available when needed.
Visibility is becoming an increasingly important concern with the current state of supply chains. A real-time asset tracking system allows the company to have a timeline. An RTLS shows where parts and materials are and streamlines processes to reduce bottlenecks. Supply chain problems force many manufacturers to discover new ways to manufacture parts, such as additive manufacturing or implementing an automated system.
Increase Your ROI by Investing in AirFinder OnSite
- Low Cost. AirFinder OnSite XLE is a fraction of the cost of competitors' pricing.
- Long Battery Life. XLE lasts up to 7 years with hundreds of location updates daily.
- Increased Efficiency. Spend less time looking for assets, and more time being productive.
Which Processes Can RTLS Improve?
There are various aerospace use cases that RTLS can resolve:
- Tool Management: Lack of tool location knowledge is a significant issue for mechanics in aerospace manufacturing. Tools are easily lost or misplaced in large facilities leading to employee hoarding, which worsens the issue. Searching for lost tools wastes hours of valuable production time. Knowing tools' location improves production time in an industry with many intricate and specific processes. RTLS provides real-time location information for each tool or set of tools.
- Assembly Optimization: Production of aircrafts in aerospace manufacturing moves in stages, so knowing when each step of the process can be completed will make the entire process more efficient. Manufacturing parts for a plane, missile, or spacecraft involves many small steps that require pinpoint accuracy. Using RTLS can expedite WIP and reduce downtime.
- Foreign Object Debris Location: Foreign object debris is any item that has been misplaced and can cause harm to humans, the nearby environment, or the item being manufactured. Planes and other aircraft types are massive, and a small tool or item left inside after manufacturing or routine maintenance could easily be overlooked. When the engine turns on, this can be deadly if the items become projectiles. If tools inside an aerospace manufacturing facility are misplaced in this manner, they become foreign object debris. If the tools are tracked with an RTLS system, they can easily be tracked and reduce the risk of injury to workers or damage to the aircraft. Using an RTLS keeps workers safe and reduces harm to aircrafts worth millions of dollars.
- Quality Control: In an industry where high standards are required, a tracking system can automate specific components. There are currently over 1400 standards in aerospace that must be adhered to. With this in mind, every process must be run as smoothly as possible. RTLS can provide location updates based on location in a facility so the next process can begin. Automatic scanning allows each task to be mapped out in the facility and gives additional time for workers to complete other tasks instead of manually scanning barcodes. Overall, RTLS provides automation and allows workers to focus on maintaining the high quality required to maintain aerospace standards.
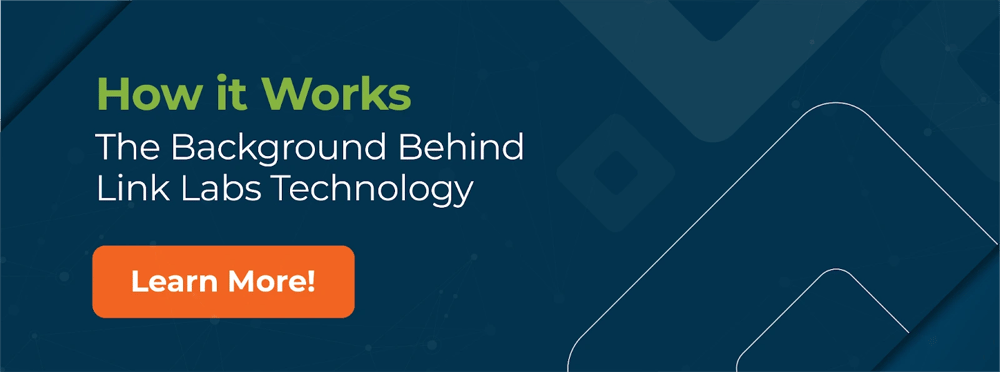
Which RTLS Technology Should You Choose?
The real-time location technology needed for manufacturing requires a system for short-range radio frequencies. The technology that uses short-range frequencies is ultra-wideband (UWB), Bluetooth, and XLE. The obvious question is, which technology is best for you?
The first step is to determine how much accuracy will be needed. Large metallic buildings (such as aerospace manufacturing plants) can distort radio frequencies and decrease accuracy. If high-level accuracy is vital to your company, choosing the right technology is essential.
UWB: UWB is a low frequency, wide radio frequency range. UWB has high location accuracy, up to 10-30 cm. With high accuracy comes a high cost. The installation, technology, and hardware tend to be more expensive. Even more, UWB waves are absorbed by metal, making the environment difficult to monitor location.
Bluetooth Low Energy: Bluetooth LE is a type of Bluetooth technology that operates in the 2.4 GHz range. This technology is typically favored because it consumes less energy than traditional Bluetooth. With less energy being used, batteries last longer. A device using Bluetooth LE will be dormant unless a connection is initiated. Batteries running on Bluetooth LE can last up to 3-5 years, depending on usage. Bluetooth LE is a great option for a manufacturing environment because it can operate in various ranges. Manufacturing environments involve indoor and outdoor components that rely on tracking devices to monitor processes. Bluetooth LE is proximity-based location technology. Manufacturing facilities are large and an RTLS system must be able to operate throughout the entire building. Tags operating on Bluetooth LE can be placed anywhere and operate with the same efficiency and accuracy.
XLE: Xtreme Low Energy (XLE) is a technology developed by Link Labs with enhanced battery life and accuracy capabilities compared to Bluetooth LE. Link Labs has also developed phase-ranging technology, which uses nearby beacons and the response time for a tag to send its location. The tag sends location updates based on the closest beacon, and this information is sent to the end user for their viewing. The longer battery life comes from location updates sent by the specifications set by the user. Batteries on XLE tags can last nearly seven years.
AirFinder OnSite
Companies involved in aerospace manufacturing could benefit from using AirFinder OnSite. AirFinder OnSite is an RTLS solution that uses patented technology to provide a seamless solution for all of a company's tracking needs. It utilizes Bluetooth LE or XLE technology to provide up-to-meter level accuracy so aerospace manufacturers can monitor tools, optimize processes, and monitor quality and foreign debris. AirFinder OnSite best suits indoor environments and uses patented technology to determine location. To learn more, book a demo.